Ion Nitriding
Ion Nitriding Instrument
The ion nitriding method was invented by B.Berghaus, Germany, in 1932, and started to be put to practical use in German and Swiss companies around 1967. NDK quickly noticed this new heat treating method. As a result of our own research, we developed the first ion nitriding instrument in Japan in 1973, and started manufacturing and consigned processing services. Currently, our JIN series are the world's top selling products and are highly regarded for their stable performance, high reliability and usability.
We provide instructions and advice for users regarding processing technologies, according to the originally developed processing techniques and rich technical data as well as a full range of customer services, such as maintenance to meet customers' needs.
JIN-10SH ion nitriding system ; auto trasport line
Rotor(turbo charger parts)SACM645
Yoke/flange(machine parts) SCM435
Advantage
feature1The nitriding processing using ionized nitrogen gas does not involve any chemical reactions and provides a clean working environment without the need for special anti-pollution equipments.
feature2Utilizing the sputtering reaction of the ionized gas largely reduces the operation time compared with the conventional nitriding processing.
feature3Direct heating by glow discharge realizes an even temperature distribution without conventional additional heating or warming devices. The heating efficiency is improved by a factor of two or more, which contributes to energy saving.
feature4Extremely small gas consumption reduces the running cost.
feature5The nitriding processing can be performed at 380 ?C or higher. For titanium, etc., the high-temperature processing of 850 ?C can also be performed.
feature6Because of the vacuum processing, the processed surface can be obtained in a nonoxidized state with little deterioration of the surface roughness. Additionally, a low temperature processing produces very little distortion and does not require any post-processing, which is ideal for processing the finished product.
feature7By adjusting the gas ratios of N2, H2, and X, the composition of the compound layer can be adjusted selectively.
The desired mechanical properties can be obtained according to the purpose.
feature8The best condition for nitriding can be selected according to the material and the pre-processing. Nitriding masking can be performed easily.
Ion nitriding instrument standards
Model | JIN-1SB | JIN-3SC-A | JIN-3SC-B |
---|---|---|---|
Input power[V(three phases)‐kVA] Thyristor method DC pulse method |
200-20 200-24 |
200-45 200-55 |
200-45 200-55 |
Output power[DC V×A] | 800×13 | 800×35 | 800×35 |
Inside dimention of furnace body [mm] (Dia.×HorL) |
500×600 | 700×1000 | 800×1000 |
Maximum treatment capacity [kg][m² (including fixtures)] | 100 0.65 |
300 1.75 |
300 1.75 |
Temperature control method | Automatic temperature control method using infrared radiation thermometer. |
Model | JIN-6SB | JIN-10SB | JIN-10SC | ||||||
---|---|---|---|---|---|---|---|---|---|
Input power[V(three phases)‐kVA] Thyristor method DC pulse method |
200-90 200-110 |
200-140 200-170 |
200-140 200-170 |
||||||
Output power[DC V×A] | 800×75 | 800×130 | 800×130 | ||||||
Inside dimention of furnace body [mm] (Dia.×HorL) |
910×1500 | 910×2500 | 1300×1225 | ||||||
Maximum treatment capacity [kg][m² (including fixtures)] | 1000 3.75 |
2000 6.5 |
2000 6.5 |
||||||
Temperature control method | Automatic temperature control method using infrared radiation thermometer. |
Model | JIN-10SH | JIN-15SB | JIN-20SB | ||||||
---|---|---|---|---|---|---|---|---|---|
Input power[V(three phases)‐kVA] Thyristor method DC pulse method |
200-140 200-170 |
200-210 | 200-280 | ||||||
Output power[DC V×A] | 800×130 | 800×188 | 800×250 | ||||||
Inside dimention of furnace body [mm] (Dia.×HorL) |
1200×1600 | 1300×2000 | 1300×3000 | ||||||
Maximum treatment capacity [kg][m² (including fixtures)] | 2000 6.5 |
3000 9.4 |
3000 12.5 |
||||||
Temperature control method | Automatic temperature control method using infrared radiation thermometer. |
※Specification may be revised without notice as improvements are made.
JIN-3SC-C ion nitriding system
Connecting rod die(for hot forging)of precipitation hardening steel
Crank die(for hot forging)SKD61
Ion Nitriding Method
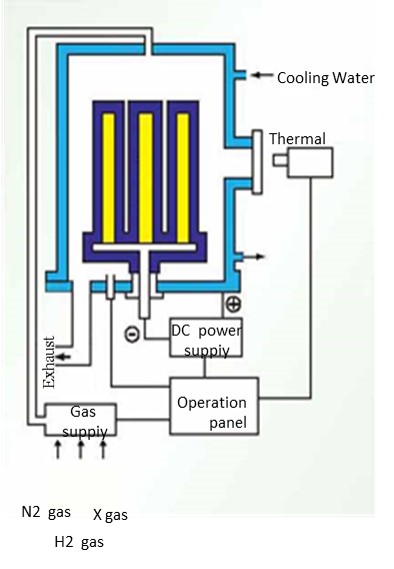
In a nitrogen gas mixture atmosphere at 13.3 Pa to 1.3 kPa, where the furnace is the positive electrode and the processing target is the negative electrode, applying a DC voltage of several hundred volts causes a glow discharge. A soft light similar to a neon light covers the processing target object. At this step, the ionized gas component is rapidly accelerated and collides with the surface of the processing target causing heating. At the same time, nitridization proceeds due to the sputtering effects.
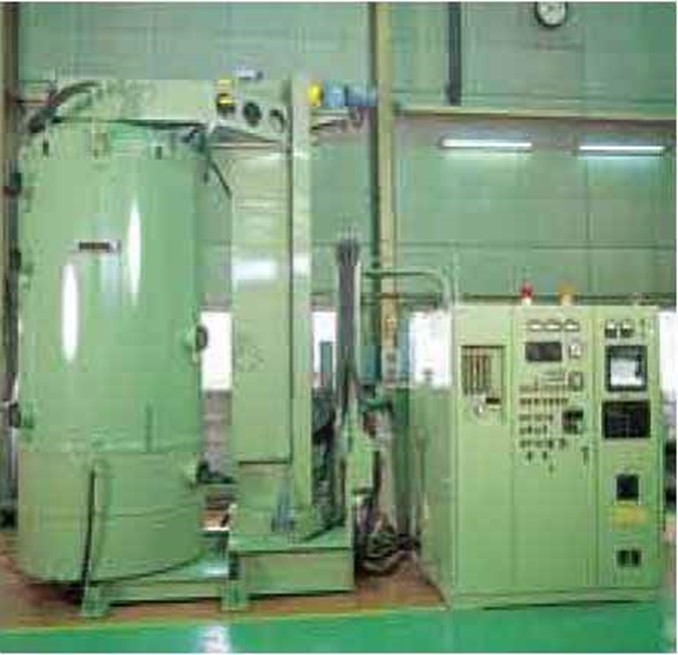
JIN-10SC ion nitriding system
As described above, ion nitriding is an innovative processing method, completely different from the conventional ones using ammonia decomposition gas or cyanide, and is currently applied to various mechanical parts such as auto parts, precision parts, injection molding machine parts, various dies, etc.
JIN-20SB ion nitriding system
Microstructures after ion nitriding
Hardness profiles after ion nitriding